The term “Pipe Stress Engineer” as used in this document refers to that person responsible for insuring that the pipe routing done by the piping layout designer is consistent with the allowables in the applicable piping Code. This includes; the thermal forces and the live and dead loads the piping system imposes on equipment, equipment nozzles and structures. The Pipe Stress Engineer is also responsible for the selecting and specifying stress related products including various types of Expansion Joints, Constant Support Spring Hangers and Snubbers or Struts.
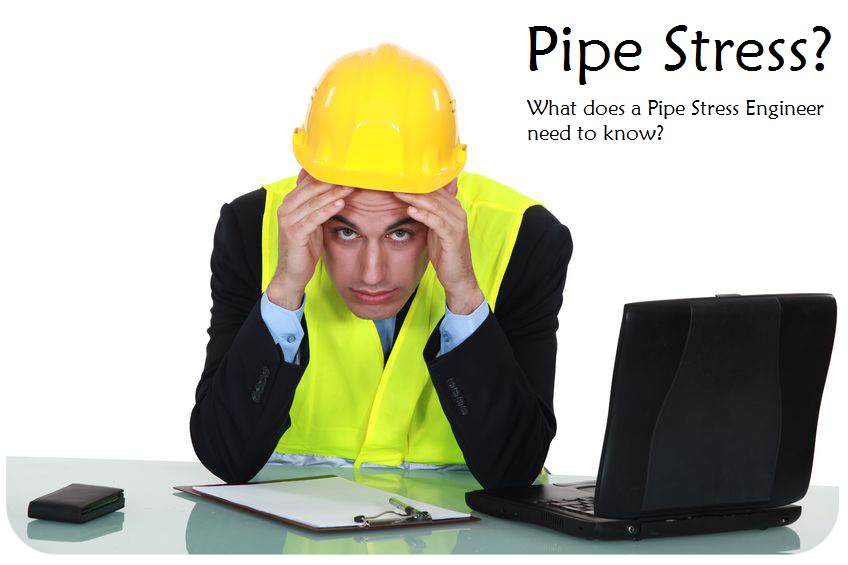
What does the Pipe Stress Engineer need to know?
Pipe Stress Engineering is more than just knowing how to turn on the Analysis software in the computer, how to find the menus and the difference between pass and fail. So, appropriately, what else does the Pipe Stress Engineer need to know about piping?
Here is a list of the most basic of things that a good Pipe Stress Engineer should know. Thinking about every one of these items should become as natural as breathing for a good Pipe Stress Engineer.
- Piping Codes – All Pipe Stress Engineers need to know about the applicable Piping Codes for the different types of Process Plants and have access to the most up-to-date copy so the proper data is used and proper decisions can be made for the calculations and the good of the project.
- Pipe, Fittings, Flanges and Valves – All Pipe Stress Engineers need to know and understand the broad spectrum of items that make up the “vocabulary” of the piping language. This includes the many types of fittings, the many different schedules, the wide variety of common piping materials, the flange class ratings and the types of the different valve designs.
- Relationship of other Engineering groups – All Pipe Stress Engineers need to know and understand the relationship, activities and contribution of all the other engineering and design groups on the project. These include: Process, Civil, Structural, Mechanical Equipment, Vessels & Tanks and Instruments/Control Systems. These groups have a responsibility for contributing to Piping’s success just as the effort of the Pipe Stress Engineer also has a responsibility for contributing to their success.
- Piping Execution – All Pipe Stress Engineers must understand how pipe stress progress is linked to P&IDs, Plot Plans, equipment vendor drawings, instrument vendor drawings and structural support design in order to understand areas where the Project may be impacted.
- Process Variables – All Pipe Stress Engineers must know and understand the four basic process variables: pressure, temperature, flow and level, and the effect these have on a piping system.
- Process Plant Equipment – All Pipe Stress Engineers need to know and understand the different types of equipment. They also need to know and understand the pipe stress related issues that effect each type of equipment.
- Equipment Operation and Internals – All Pipe Stress Engineers need to understand the equipment process function and the equipment internals in order to give proper consideration to the effect of piping connected to and reacting on the various nozzles/connections.
- Equipment piping – All Pipe Stress Engineers need to know the right and the wrong way to pipe up (connect pipe to) different kinds of equipment and for maintenance/disassembly space requirements. This includes pumps, compressors, exchangers, filters or any special equipment to be used on a specific project.
- Allowable pipe spans – All Pipe Stress Engineers need to know and understand the span capabilities of pipe in the different schedules for a wide variety of common piping materials. When a new project introduces a new material with severely reduced span capabilities; supplemental training may be required.
- Expansion of pipe – All Pipe Stress Engineers needs to understand that they should treat a piping system as though it is alive. It has a temperature and that temperature causes it to grow and move. That growth and movement must be allowed for and incorporated in the overall design. Not just of that specific line but for all other lines close by. The process of expansion in a pipe or group of pipes will also exert frictional forces or anchor forces on the pipe supports they come in contact with.
- Routing for flexibility – All Pipe Stress Engineers must understand that the piping layout designer has routed the pipe for flexibility and support. Routing for flexibility can normally be achieved through the most natural routing of the pipeline from its origin to its terminus. Routing for flexibility means (a) do not run a pipe in a straight line from origin to terminus and (b) building flexibility into the pipe routing is far cheaper and more reliable than expansion joints.
- Weight and loads (live loads and dead loads) – All Pipe Stress Engineers need to be able to calculate and analyze the effects of weight and loading. They need to know and understand that everything has a weight. They need to be able recognize when there is going to be a concentrated load. They need to have access to basic weight tables for all the standard pipe schedules, pipe fittings, flanges, valves for steel pipe. They also need to have the weight tables for other materials or a table of correction factors for these other materials vs. carbon steel. They need to be able to recognize when downward expansion in a piping system is present and is adding live loads to a support or equipment nozzle.
- Standards and Specifications – All Pipe Stress Engineers need to understand the content and application of the client and engineering company Standards and Specifications used on the project. In particular the Pipe Stress Engineer must have intimate knowledge of the primary Standards and Specifications he/she will use; these being the Misc. (or Secondary) Pipe Support Standards and Piping Material Line Class Specifications.
- Vessel piping – All Pipe Stress Engineers also need to understand about the connecting, supporting and guiding of piping attached to vessels (horizontal or vertical) and tanks. They need to know that nozzle loading is important and does have limitations.
- Rack piping – All Pipe Stress Engineers need to understand that there is a logical approach to the placement of piping in (or on) a pipe rack and the setting of rack elevations. It does not matter how wide or how high the rack or what kind of plant, the logic still applies. Starting from one or both outside edges the largest and hottest lines are sequenced in such a manner that allows for the nesting of any required expansion loops. Another good guideline is; Process lines on the lower deck(s) and Utility Lines on the upper deck(s). The spacing of the lines must also allow for the bowing effect at the loops caused by the expansion. One rule of thumb for setting the distance between piping levels is three times the largest pipe size.
- Expansion loops – All Pipe Stress Engineers need to understand and be able to use simple rules, tools and methods for checking loops in rack piping. This should include the most common sizes, schedules and materials. They also need to be able to calculate forces of individual line anchors and the combined forces of all lines at a specific support.
- Cold spring/Pre-spring – All Pipe Stress Engineers should understand the basics rules of cold spring and pre-spring. They need to understand what each one is along with when to and when not to use each.
- Design production methods – All Pipe Stress Engineers need to be able to read of the various types of piping documents (manual or CAD sketches, layouts, detail piping plans, isometrics, etc). Every Pipe Stress Engineer must also be able to go to the field or sit in front of a client and make proper, intelligent, and understandable pipe stress decisions. They must also be able to produce detailed final analysis packages. Today, Pipe Stress Engineers also need to know (or be able to learn) a wide range of electronic 2D or 3D design tools.
- Heat Tracing – All Pipe Stress Engineers need to understand the effect of process heat conservation, know the different methods (Jacketing, Tracer Tubing or Electric), Tracer commodity (Steam, Oil, Hot Water, etc.) and Tracer system requirements and be able to consider the heat tracing in the analysis process.
- Deliverables – All Pipe Stress Engineers need to understand the purposes of each of the Pipe Stress deliverables, such as Specifications, Data Sheets, and System for individual line analysis packages, Pipe Sress Logs, Vendor Drawings (Expansion Joint, Spring Hangers and Struts).
- Stress Sketch Content – All Pipe Stress Engineers must understand how to present their comments and instructions. Stress Sketches become a part of the Legal Records for the Project. Therefore all notes and comments on Stress Sketches must be well thought out and clearly written in order to clearly communicate the required and agreed to changes to the design.
- Economics – All Pipe Stress Engineers must be aware of economics. Adding Expansion Joints at the expense of increased maintenance may not be the most cost effective solution to a perceived stress problem.
Any person that has this type of training, this type of knowledge and then consistently applies it is indeed a Pipe Stress Engineer.
He or she will also be a more valuable asset to their company and to themselves in the market place.
Reference:- www.PipingDesigners.com
http://pipingdesigners.com/contents/blog/33-blog-1h-what-does-a-pipe-stress-engineer-need-to-know.htmlReferenced Post :- PipingDesigners.com
Contact Info:-
E-Mail:- timmsvillee@gmail.com
No comments:
Post a Comment